UHMWPE UD continuous orthogonal vulcanization Crossply Machine
The Crossply machine cuts segments from the UD material, aligns them in the desired orientation—typically 0/90°—and compresses them together. The machine consists of components such as the 0° unwinding device, the 90° unwinding device, the width adjustment device, the pressing and laminating device, and the rewinding device, among others. It can be used for pressing and laminating 2/4/6/8 UD fabrics. This method enhances reinforcement efficiency, resulting in lighter and thinner technical textiles.
The Crossply machine represents a significant advancement in manufacturing technology, offering unparalleled performance, versatility, and sustainability. With its advanced features and innovative design, it is the ideal solution for manufacturers looking to boost their production capabilities and stay ahead of the competition. Experience the future of manufacturing with the Crossply machine.
Machine Features
Powerful Hydraulic Pressing System
The 6000KN four-cylinder hydraulic system operates on a 1700 x 1700mm lamination table. It is equipped with HMI and PLC controls for precise pressure adjustment, acceleration, pressure holding, and other essential functions.
Advanced 0° UD Tension Reel
The 0° UD three-axis tension reel can hold up to three rolls of UD material, ensuring efficient and smooth unwinding.
High-Precision 90° UD Tension Reel
The 90° UD tension reel uses pneumatic clamping combined with a servo motor for lateral movement, preventing deformation or misalignment of the UD material. Fragment sizes can be directly set and adjusted on the touchscreen.
Servo-Driven Longitudinal Adjustment
Laminated products are pulled by servo rollers for precise longitudinal adjustments, enabling tension winding to produce high-quality UD composite fabric rolls.
Multi-Point Pneumatic Pressing Structure
The pneumatic structure of the multi-point upper pressure plate ensures consistent clamping force across all points, allowing for quick and uniform pressing.
Thermal Knife for Precise Cutting
The system uses a thermal knife to achieve accurate transverse fragmentation of materials.
Durable and Reliable Track System
The moving track surface undergoes high-frequency quenching and hard chromium plating, significantly increasing durability and service life.
Advanced Surface Treatment for Durable Moving Tracks
High-frequency quenching and hard chromium plating are applied to the moving track surface, ensuring a long service life with excellent performance.
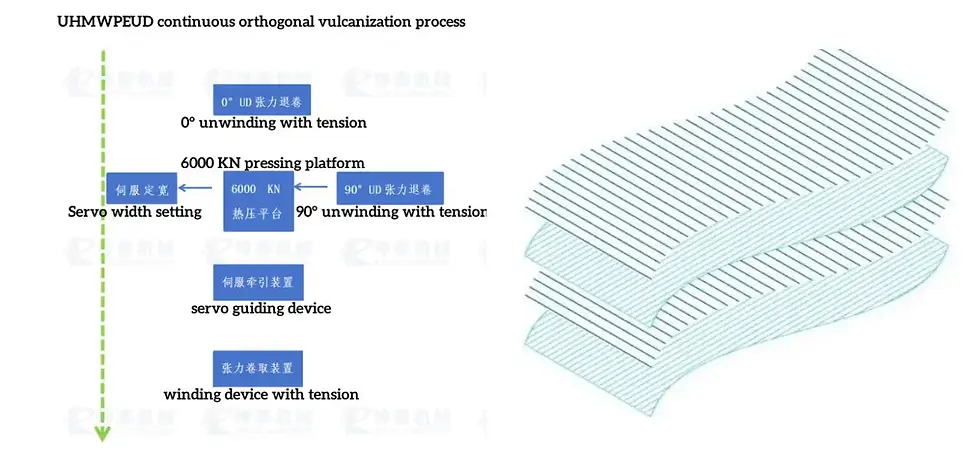
Main Machine Parameters (Customizable)
Material width | ≤ 1650mm |
Pressing tonnage | 6000KN |
Heat source medium | Thermal oil |
Pressing method | Hydraulic |
Control mode | HMI+PLC |
Transmission control | Variable frequency+servo drive |
Total power | 90KW |
Power supply | 380V/50Hz |
Length * width * height | 9500 * 7500 * 5000mm |
Working table dimension | 1700 * 1700mm |
Fabric Sample
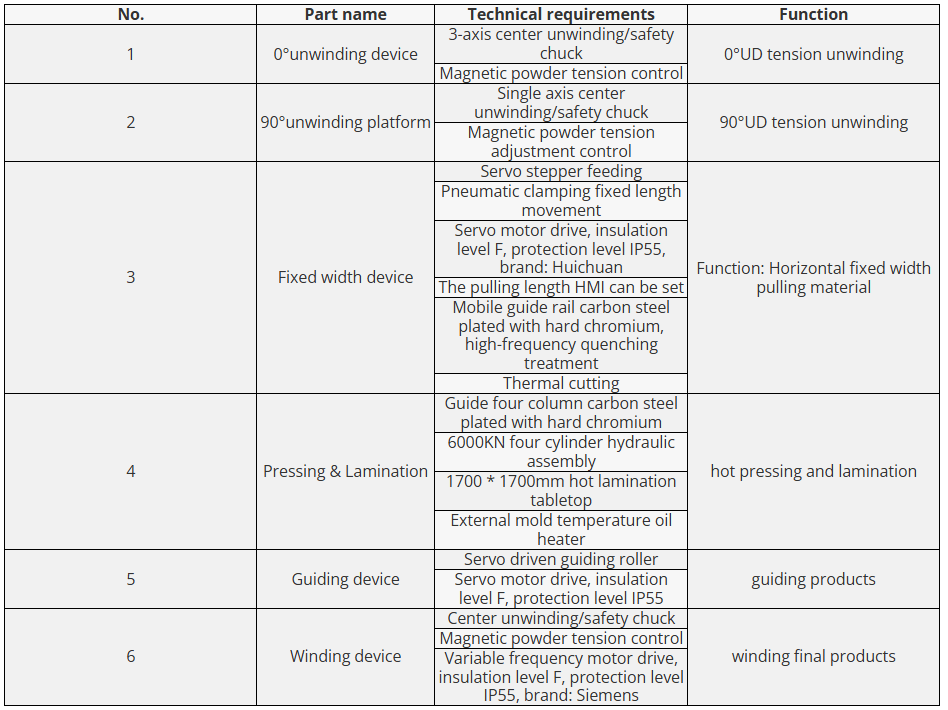
Fabric Sample
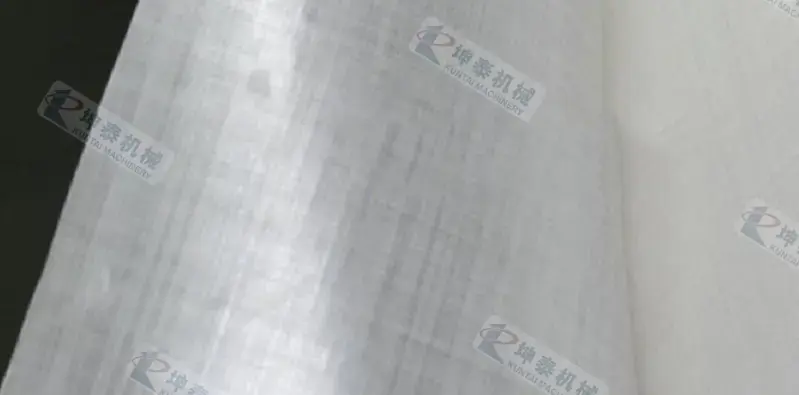
Crossply Machine working process:
-
Feeding the unidirectional PE UD onto the 0° and 90° tension unwinding devices.
-
The 0° UD fabric is fed with tension to the hot pressing platform by the servo traction device.
-
After the 90° UD fabric is pulled and reaches the servo width setting position, it is cut by the hot cutting device.
-
The upper hot pressing head is quickly pressed down, and the pressure is transmitted through signal sensing to drive the composite.
-
The servo traction is used in conjunction with the tension shaft to roll the PE UD orthogonal finished fabric.